Reportage: r&d-tak vestiging Den Bosch leidend bij tech-ontwikkelingen Omron
Omron kan bogen op productiecapaciteit in Italië en Nederland. Om de flexibele productieoplossingen te tonen, organiseerde de Japanse technologieleverancier een fabriekstour in Den Bosch. Artificial intelligent (ai), data-science, elektronisch vernuft en de zoektocht naar veilige communicatie vormen de ingrediënten voor een maaltijd, bereid door een Tim Foreman, een Nederlandse r&d-chef in een Japanse keuken. Waarbij de bedrijfsfilosofie er niet vanuit gaat om de mens geheel te vervangen door machines.
De hype rond ai draagt bij aan het misverstand dat een ai-project zich met de beschikbaarheid van generatieve-ai-chatbots snel laat optuigen. Tim Foreman, r&d-manager bij Omron in ’s-Hertogenbosch, weet uit ervaring dat niet de tools doorslaggevend zijn. Belangrijker is de beschikbaarheid van opgeschoonde, gestructureerde data. Hij haalt een studie van IBM aan, waarin werd vastgesteld dat de helft van alle projecten in de wereld stoppen omdat het opschonen van data te veel tijd en moeite kost. ‘Wij ontwikkelen en maken hier machines voor industriële automatisering. Wij zien ons dus geplaatst voor het vraagstuk om data te verzamelen voor uiteenlopende doelgroepen: variërend van shiftleaders en onderhoudsspecialisten tot aan directieleden. Daartoe willen we de door de machines geleverde data omzetten naar informatie. Die machines zijn nooit bedacht met functionaliteit om hun data gestructureerd samen te vatten op een manier waardoor ze zich lenen voor managementinformatie, laat staan voor data-science of ai-toepassingen. Bij het ontwerpen en verkopen van nieuwe automatiseringsproducten houden we daar dus rekening mee. Wie over een al wat ouder machinepark beschikt, zal eerst veel tijd moeten steken in het netjes structureren van de data. Dat is niet eenvoudig, ook al omdat je het productieproces niet kunt stilzetten om nieuwe functionaliteit in te bouwen en te testen.’
Robots
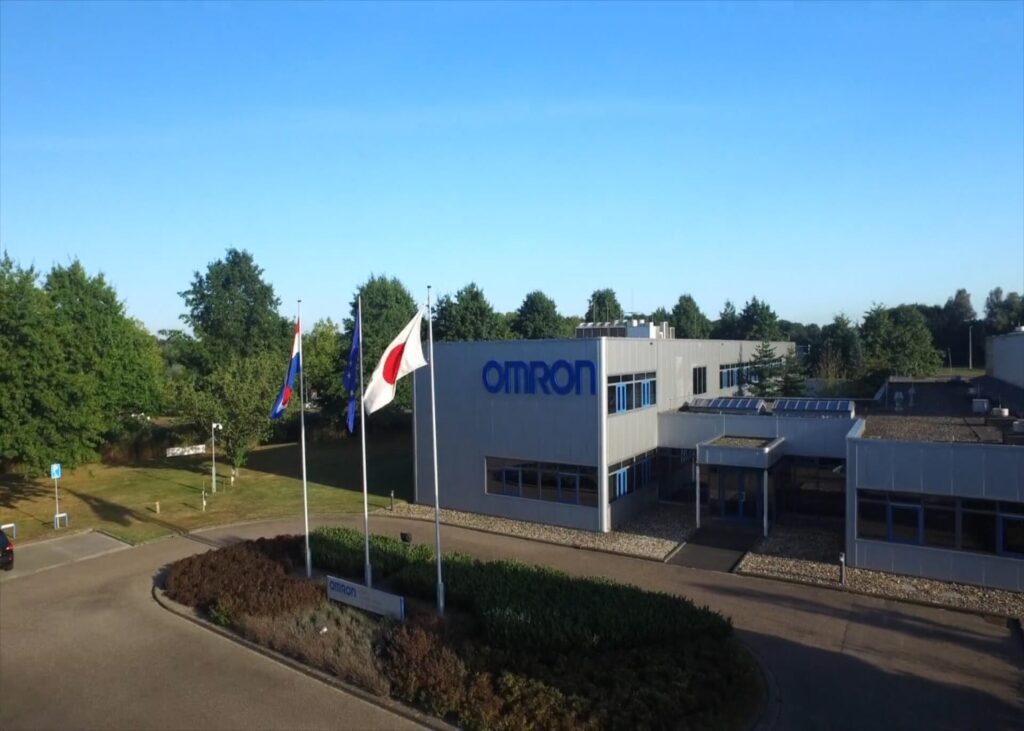
Omron heeft naast een reparatiecentrum ook een productiebedrijf in Den Bosch voor industriële robots, pc’s, plc’s en controllers. Hoewel de Japanse onderneming bekendheid geniet door het aanbod van medische instrumenten, vertegenwoordigt deze activiteit maar nog geen twintig procent van de omzet, terwijl bijna zestig procent voortkomt uit de productie van apparaten en systemen voor industriële toepassingen. Zowel de productieprocessen als de logistieke activiteiten in een fabriek hebben de aandacht van de Japanners, die in 1933 van start gingen met medische precisie-technologie. Het bedrijf wil zich onderscheiden met een mensgerichte bedrijfscultuur. In 1959 formuleerde oprichter Kazuma Tatseisi de ondernemingsmissie als volgt: werken voor een beter leven en een beter leven voor allen. En nog steeds toetst men de ontwikkelinspanningen aan dat motto. Productiemachine en robots worden in de eerste plaats gemaakt om menselijke arbeid te ondersteunen. De bedrijfsfilosofie gaat er niet vanuit om de mens geheel te vervangen door machines.
Het teamverband staat centraal bij het oplossen van de knelpunten in de eigen productieprocessen. Foreman geeft een voorbeeld. Op een productielijn waar printed circuit boards (pcb’s) zich laten ’bestücken’ met componenten, zorgt een proces van ’soldeerpastadepositie’ voor het snel aanbrengen van een laag soldeermateriaal aan één zijde van de pcb. Daarna controleert omwille van de snelheid een automatisch inspectiesysteem of het soldeerproces goed is verlopen. Toen er zich haperingen voordeden, hadden de betrokken operators geen idee waaraan dat lag. Volgens Foreman waren er te veel aspecten waarop het mis kon gaan, terwijl het detectiesysteem niet voorzag in data met een gedetailleerd overzicht van het inspectieproces. Capaciteit om het probleem op te lossen, was er niet. ‘We stelden een student data-science aan om de zaak uit te zoeken. Na twee weken kwam de student met een verrassende conclusie waaraan de operationele medewerkers nooit hadden gedacht. Op basis van die bevindingen voegden we aan de inspectiemachine software toe die via een scherm tot op component niveau met tijdsaanduiding de inspectieprocedure visualiseert.’
Andere partijen
De inspectiemachine wordt door Omron ook aan andere partijen geleverd. Voor de rest verkopen ze alleen componenten, zoals sensoren, controllers, plc’s en industriële pc’s waarmee ook concurrenten industriële automatiseringssystemen samenstellen. Zelf werkt de fabrikant in Den Bosch ook samen met toeleveranciers. Zelfs uit de nabije omgeving, want op een exemplaar van een recent model autonome mobiele transportrobot staat duidelijk de naam Actemium als maker van het draaglastdeel. Anders dan bij de zogeheten ‘automatic guided vehicle’ navigeert een mobiele robot zonder dat er geleiders in de vloer zijn aangebracht. Omron maakt ze met een draaglast variërend van negentig tot 1.500 kilogram. Voorzien van sensoren, procesoren en andere elektromechanische componenten vinden ze zelfstandig de weg door fabrieken en magazijnen, ongeacht of daarin zich mensen of andere objecten bevinden. Uitgerust met camera’s zien ze wat ze doen en waar ze naar toe gaan. Het bedrijf schroomt niet om ze zelf ook toe te passen op de werkvloer. Ook als de ruimten tussen de diverse werkcellen met zowel personen als robots drukbezet zijn wachten de wagentjes geduldig op een vrije baan of weten ze de obstakels te ontwijken door handig om te rijden.
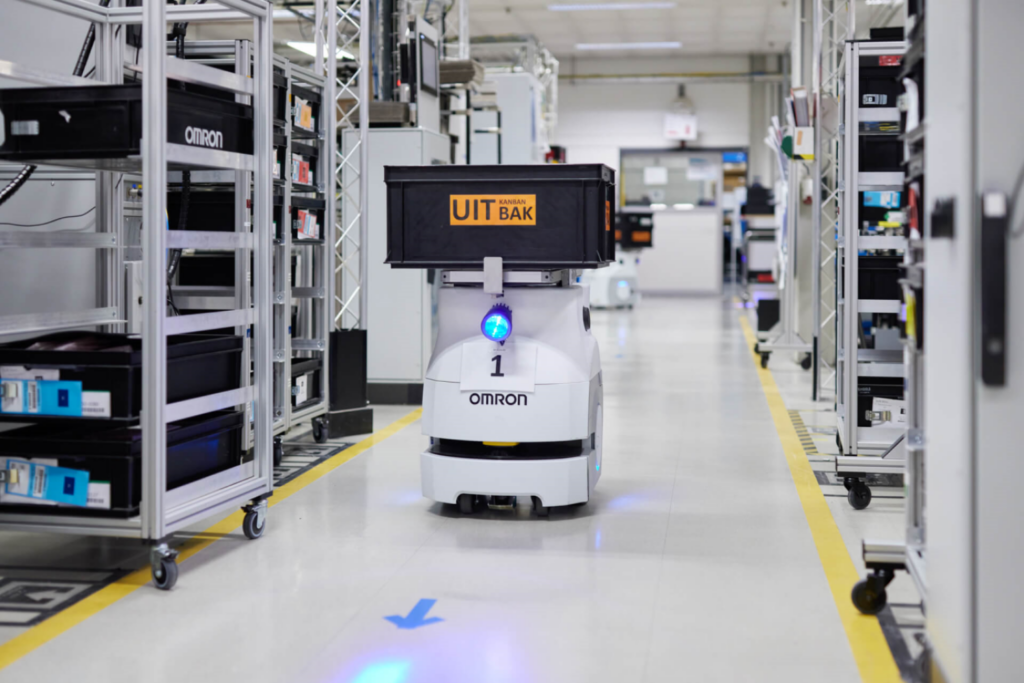
Met de vele stuursignalen en andere vormen van dataoverdracht tussen de productiemachines en de servers in de controleruimte, staat cyberbeveiliging hoog op de agenda. Op dat vlak fungeert de r&d-afdeling in Den Bosch als speerpunt voor de wereldwijde Omron-organisatie. Die gidsfunctie heeft te maken met de geringe geografische afstand tot Brussel. Daar nam de EU-organisatie initiatieven voor cyberbeveiliging zoals de NIS-2-richtlijnen en de Cyber Resilience Act, waarmee Europa vooroploopt in het verankeren van maatregelen voor cyberweerbaarheid in de wetgeving. Ook de interoperabiliteit tussen de verschillende machines van uiteenlopende fabrikanten heeft de aandacht van de afdeling.
Foreman maakt zelf deel uit van het standaardisatiecomité met 24 andere partijen rond het communicatieprotocol OPC UA FX. De laatste twee letters staan voor field exchange. ‘Industriele netwerken, gebaseerd op het OPC UA-protocol zijn weliswaar open en maken dus aansluiting van elk apparaat mogelijk, maar garantie dat beide apparaten probleemloos werken is er niet’, aldus Foreman. ‘Iedereen kan de standaard anders interpreteren. FX integreert ’time sensitive networking’, afgekort TSN, waarmee de standaard realtime-operaties faciliteert. Straks kan je kiezen voor netwerken met of zonder TSN, maar in beide gevallen is operabiliteit gegarandeerd’.
Milliseconden
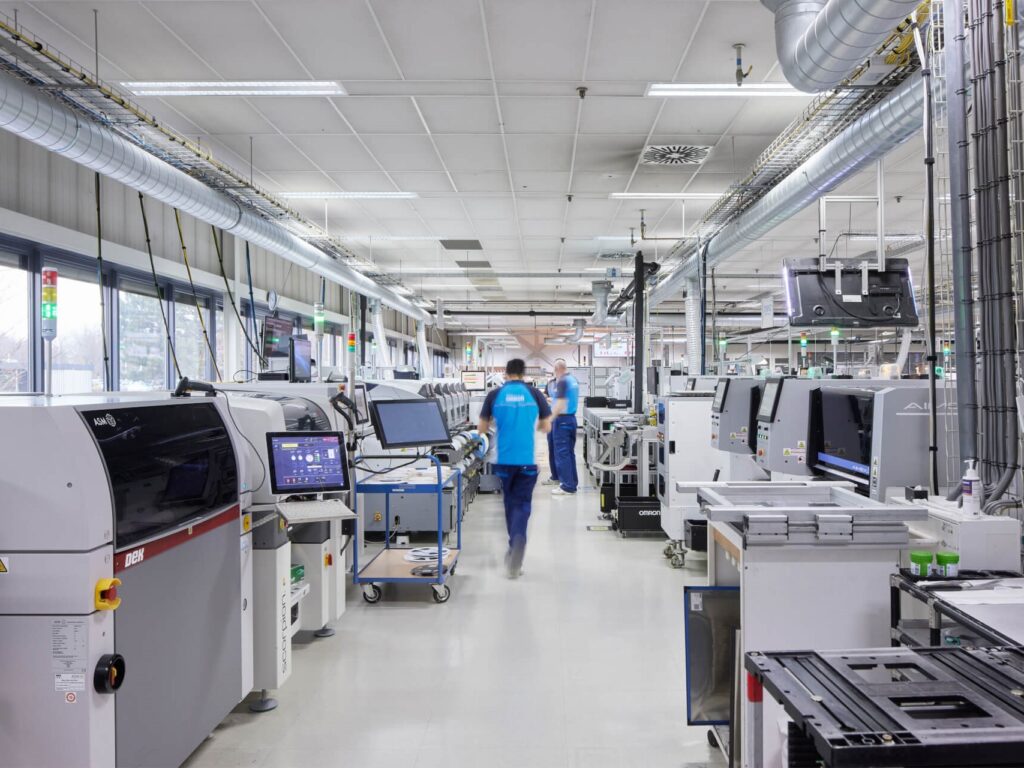
De r&d-baas van Omron Europa weet te vertellen dat eerste versie van de standaard is uitgebracht voor controller-naar-controller-communicatie met monitoringfunctionaliteit in milliseconden of sneller. ‘De volgende versie voor de communicatie tussen controller en apparaat laat nog een aantal jaren op zich wachten’, zegt Foreman. ‘Het schrijven en valideren van een standaard om de grote verscheidenheid aan apparaten aan elkaar te knopen en te synchroniseren kost nu eenmaal tijd. Demo-opstellingen van de standaard zijn al wel beschikbaar in Europa, Azië en Amerika’.
Overigens ziet hij op het vlak van de draadloze communicatie ook nog uitdagingen. Binnen de huidige draadloze fabrieksoplossingen is wifi de meest gebruikte vorm. In samenwerking met Nokia experimenteert Omron met 5G-signaaloverdracht waarmee de positiebepaling van robots veel nauwkeuriger wordt. Het wachten is op de commerciële beschikbaarheid van de 5G-frequenties met de gewenste capaciteit. Ondertussen profiteert men van de capaciteitsverbetering van Wifi 6. Bluetooth speelt geen rol binnen de fabrieksautomatisering vanwege de geringe afstanden die deze technologie kan overbruggen.
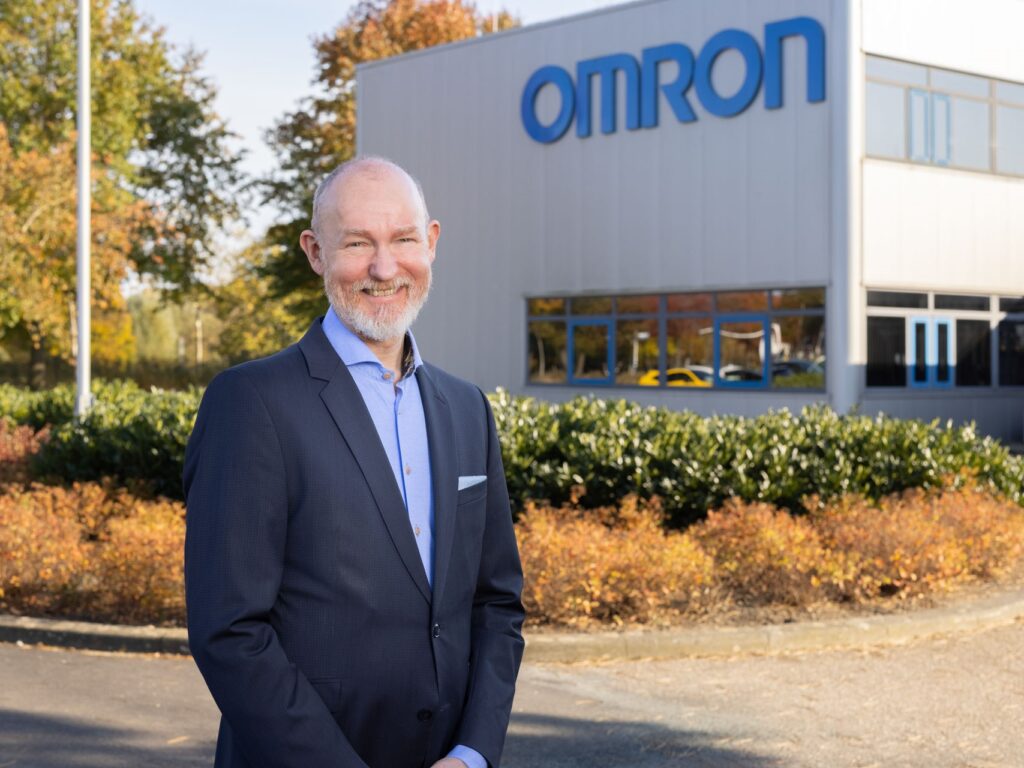
Samenwerking JADS
Ook op het gebied van ai en data-science speelt de Omron-fabriek in Den Bosch een voortrekkersrol binnen het concern. De r&d-afdeling weet zich gesteund door de nabijheid van de Jheronimus Academy of Data Science (JADS), waarmee een hechte samenwerking is opgebouwd. De wereldwijde afnemers van de Japanse fabrikant mogen rekenen op de adequate steun van een helpdesk bij het in gebruik nemen van een apparaat of het doorgeven van storingen. Voor elk model binnen de productlijn bestaan handleidingen.
Inmiddels is de inhoud van ruim vierduizend handleidingen omgezet naar een ai-toepassingen, die helpdeskmedewerkers ondersteunen bij het snel en adequaat uitvoeren van hun taak. Andere vormen van algoritme-ontwikkeling moeten leiden tot het effectief meeliften op de ontwikkeling van nieuwe halfgeleidertechnologie zoals snellere cpu’s, gpu’s en inmiddels ook tensor processing unit (tpu)-processoren. Laatstgenoemde is een asic (application specific integrated circuit) voor het verwerken van Tensor Flow-software. Die moet een bijdrage leveren aan het verminderen van het energieverbruik bij het uitvoeren van intensieve ai-calculaties en algoritmen.