Digital twins maken een opmars. Het zijn digitale tweelingen van een fysiek object (of zelfs complete fabriek). Industriegigant Siemens heeft al veel ervaring met ‘computer-evenknieën’ en gaat nu een stap verder: maak een projectie van een fabrieksproces opdat tijdig is na te gaan of de meest efficiënte inrichting is gekozen.
De laatste twee jaar duikt het onderwerp digital twin regelmatig op. Er zijn bijvoorbeeld conferenties over hoe je een SAP-omgeving moet inrichten om maximaal gebruik te maken van dit nieuwe fenomeen. Kortgeleden hield Siemens Digital Industries Software, de softwaretak van het industriegrootbedrijf waarin het overgenomen Mendix is verweven, een bijeenkomst voor pers en analisten in New York onder het motto ‘Where Today Meets Tomorrow’. De softwaredivisie heeft zijn hoofdzetel in de VS. Tijdens het samenzijn in de Big Apple voerden digital twins de boventoon.
Het ontstaan van deze tweelingen vindt zijn oorsprong in de digitale transformatie. Eigenlijk is tegenwoordig alles al digitaal voordat een fysiek product wordt gemaakt. De ontwerptekeningen zijn met cad-systemen gemaakt, in 3d met geïntegreerde simulatiesoftware, zodat tijdens het design al is na te gaan welke wijzigingen een product beter maken. Fysieke modellen zijn niet meer nodig. Als je dan al een digitale weergave hebt van bijvoorbeeld een fiets, dan is het een koud kunstje om het stalen ros met sensoren uit te rusten en de data in te lezen in het computermodel. Gegevens over hoe het rijwiel in de praktijk zich gedraagt, komen zo weer in de ontwerpfase terug om het product te vervolmaken. De kwaliteitscirkel van Deming in optima forma.
Comprehensive digital twin
Siemens Mindsphere is een cloudgebaseerde toepassing die via internet of things de data van objecten, maar zelfs complete fabriekslijnen, verzamelt, aggregeert en analyseert. De combinatie met het low-code programmeersysteem van Mendix maakt het mogelijk eenvoudig extra of andere functionaliteit toe te voegen. De samenwerking tussen Siemens en AWS laat zien dat dit alles geheel in de cloud kan afspelen.
De Duitse industriegigant noemt de oplossing xCelerator: een combinatie van software, diensten en platform voor applicatieontwikkeling om de digitale onderneming vorm te geven. Dit alles leidt tot wat Siemens noemt de ‘comprehensive digital twin’: integratie tussen alle productengineering-domeinen, ‘closed loop performance engineering’, hoger innovatietempo.
Praktijkvoorbeelden
Het oorspronkelijk Israëlische Ham-Let (de Nederlandse dochter heet Astava) produceert wereldwijd industriële kleppen en hulpstukken voor pijpleidingen. Het bedrijf wilde geïntegreerde sensoren toepassen om kennis te vergaren over zijn industriële stromingssystemen, kleppen, fittings en andere (buis)componenten in de praktijk. Tegelijkertijd bedoeld om de betrouwbaarheid van de producten te vergroten en de kosten te verlagen. Sensoren meten temperatuur, druk, vibratie, geluid en luchtvochtigheid. Mindsphere en AWS laten tijdig zien of lekkages dreigen, onderhoud gebeurt als het echt nodig is; de data vloeien terug in het ontwerpproces om de producten te verbeteren.
Marco Suvilaakso, chief strategy officer bij Polar Electro, vertelt hoe de fabrikant van slimme (sport)horloges baat heeft bij digital twins om het ontwerp- en productieproces te verbeteren. Brian Sniegocki, senior analist bij Dana, producent van auto-onderdelen, vertelt dat de kwaliteit stukken hoger ligt. Lateef Khan, general manager Digital Services & Solutions bij Mercury Marine, fabrikant van buitenboordmotoren, beschrijft hoe de software ook helpt om 3d-data te delen met partners/toeleveranciers om de productie te versnellen.
Vinfast
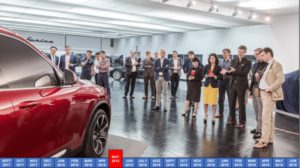
Het indrukwekkendste verhaal komt van Dave Lyon, hoofdontwerper bij Vinfast. Hij vertelt waarom en hoe de Vietnamese Vin Group besluit om een autofabrikant te worden. Zonder enige ervaring op dit vlak heeft het bedrijf een fabriek gebouwd voor de productie van 250.000 auto’s (luxe sedan en SUV) per jaar en 250.000 elektrische scooters. In twee jaar tijd van idee tot productie!
Vorm een groep van de beste bedrijven uit de auto-industrie (zoals Hella, BMW, Italdesign, Bosch, Siemens) en laat ze samen voor jou auto’s ontwerpen. Vervolgens zijn die tekeningen voorgelegd aan de Vietnamese bevolking. Er zijn twee ideeën uitgekozen en verder uitgewerkt. Tussendoor is ook nog een elektrische scooter ontworpen en gebouwd.
Ook is een complete fabriek gebouwd en ingericht. Op 15 juni 2019 was de opening van de fabriek. Het bedrijf telt nu 4.750 medewerkers. Lyon vertelt dat dit alles onmogelijk was geweest zonder digitale tools en processen van Siemens.
Virtuele productlijnen
Rene Wolf, senior vice president Manufacturing Operations Management Software bij Siemens Digital Industries Software, vindt dat de voordelen van de ‘comprehensive digital twin’ inmiddels al genoegzaam uit de doeken zijn gedaan. ‘Als we van producten succesvol een tweeling kunnen maken, dan kunnen we dat ook met de productieprocessen zelf’, is zijn stelling.
Het complete fabricageproces, inclusief voorraadbeheer en toelevering van onderdelen, wordt gedigitaliseerd. Klaar om met simulaties te achterhalen hoe processen zijn te verbeteren.
Ook hij komt met voorbeelden. Electrolux wilde achterhalen hoe ze voorraden terug kunnen brengen, vertragingen in productielijnen kunnen voorkomen en de investering voor productielijnen kunnen verminderen. Met de ‘procestweeling’ bleek het bedrijf twee miljoen dollar per jaar te besparen en een dertig procent snellere time-to-market te realiseren.
De Chinese fabrikant van auto-onderdelen Mino gebruikt de software van Siemens om virtuele productielijnen te maken. Gevolg: 30 procent reductie in projectcycli, en 35 procent sneller storingen verhelpen. Wolf heeft nog meer voorbeelden, maar waar hij verder de nadruk op wil leggen is de synchronisatie van de digital twin van het product/de fabriek met de digital twin van het productieproces. Deze twee moeten goed op elkaar zijn afgestemd om de gewenste voordelen te halen.
En dan, dan hebben we het over industrie 4.0.
Dit artikel is ook gepubliceerd in Computable Magazine 2020/#1